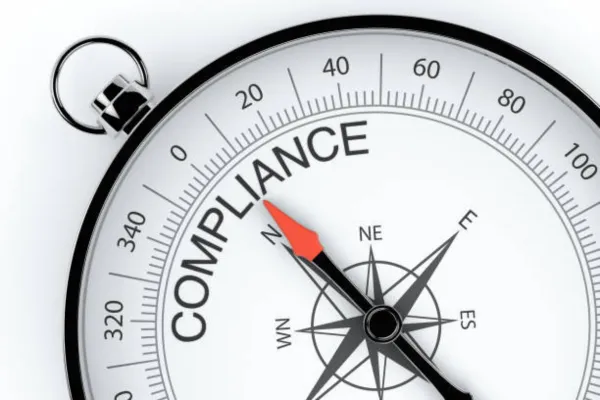
Essential Safety Standards for Gate Automation: UL 325 & ASTM F2200
In the world of gate automation, safety is paramount. Every installation, whether it's a residential gate or a high-security access point, must protect users and meet rigorous standards. For gate automation installers, access control system integrators, contractors, architects, and developers, understanding and adhering to the UL 325 and ASTM F2200 standards is crucial to delivering safe, compliant, and reliable systems.
This guide unpacks the essentials of UL 325 and ASTM F2200 standards, providing practical insights into how they impact gate automation and why they are critical for safety, compliance, and project success.
Why Are UL 325 and ASTM F2200 Standards Important?
Gate automation systems need significant force to operate heavy gates. This force, if unchecked, can create hazards such as pinch points, entrapment zones, or reach-through risks. Properly adhering to UL 325 and ASTM F2200 mitigates these risks, ensuring that automated gates operate safely around pedestrians, vehicles, and property.
These standards are designed to:
Protect users from potential harm due to mechanical or operational failures.
Provide a consistent safety benchmark for all automated gate installations.
Ensure compliance with federal and local regulations, which often require adherence to these standards.
What Is UL 325?
UL 325 is the safety standard set by Underwriters Laboratories for electrically operated gate operators. It specifically targets automated gate systems and requires that any operator used in such systems includes essential safety mechanisms to reduce risk.
The key components of UL 325 cover:
Gate Operator Classifications: UL 325 classifies gate operators based on intended usage (Class I-IV). Each class has unique safety requirements to suit the level of use and exposure to the public. For instance:
Class I: Residential, single-family usage.
Class II: Commercial or public access (e.g., parking garages).
Class III: Industrial or limited-access applications.
Class IV: Restricted access, such as military or government sites.
Entrapment Protection: UL 325 mandates that gate operators must include devices to prevent entrapment. These devices, known as “primary and secondary entrapment protection,” can vary but generally include:
Type A: Inherent reversing sensors that detect obstructions and reverse the gate.
Type B1: Non-contact sensors, such as photoelectric sensors, which stop and reverse the gate when an object is detected.
Type B2: Contact sensors, such as gate edges, which detect impact and trigger a stop or reverse action.
Continuous Monitoring and Functionality Testing: UL 325-compliant operators need to conduct periodic checks on all safety devices. If a device fails, the operator must either halt or perform restricted movement until the issue is resolved.
Signage Requirements: Clear warning signs are essential, especially for gates in public areas or with frequent foot traffic. These signs inform people of potential risks and the operational nature of the gate system.
Access Control: Operators must prevent unintended activation by unauthorized users. For example, Class I and II operators often include secure access systems that comply with UL 325 to prevent accidental or unauthorized openings.
What Is ASTM F2200?
While UL 325 focuses on the gate operator, ASTM F2200 covers the physical construction and design of the gate itself. This standard provides the guidelines for building safe automated gates, ensuring they’re designed to minimize risks and withstand repeated use.
Key elements of ASTM F2200 include:
Gate Construction and Dimensions: ASTM F2200 specifies minimum dimensions and construction standards. For example, it mandates that sliding gates must not have gaps exceeding 2.25 inches between the gate frame and adjacent structures to prevent entrapment or reach-through hazards.
Clearance and Reach-Through Prevention: This standard requires automated gates to be designed with minimal clearances that prevent reach-through injuries. For instance, the space around the gate's moving parts should be small enough to prevent fingers, hands, or limbs from getting caught.
Gate Types and Specific Requirements: ASTM F2200 addresses different gate types, including sliding, swing, vertical lift, and pivot gates. Each type has unique requirements:
Sliding Gates: Should have smooth surfaces and avoid sharp protrusions.
Swing Gates: Must have protected pinch points to prevent accidents during movement.
Vertical Lift Gates: Should incorporate specific safety measures to prevent gates from falling.
Safety Enhancements: ASTM F2200 also recommends additional safety enhancements, such as protective guards, non-contact sensors, and guide rails, especially for gates in high-traffic areas. These features further reduce risks around areas where pedestrians and vehicles frequently cross paths with gate operations.
The Practical Impact of UL 325 and ASTM F2200 on Gate Installations
Compliance with UL 325 and ASTM F2200 is more than a legal requirement—it’s a practical approach to risk management. Here’s how following these standards directly benefits installers, property owners, and end users:
Increased Safety for All Users: Compliance minimizes potential hazards, particularly in shared or public spaces. Ensuring that a gate system has both primary and secondary entrapment protections prevents severe injuries.
Enhanced Reliability and Customer Satisfaction: Systems built to standard are more reliable and experience fewer operational issues. Clients can trust that their gates will function safely and effectively, reducing callbacks and maintenance costs.
Ease of Regulatory Approval: Many jurisdictions require adherence to these standards for permitting and inspection purposes. Compliance simplifies regulatory processes and avoids costly penalties or reconstruction.
Professional Credibility: Installers who comply with UL 325 and ASTM F2200 show a commitment to best practices and industry standards. This boosts credibility and builds trust with clients and other contractors.
Ensuring Compliance: Practical Tips for Gate Automation Installers
Understand the Site’s Class Requirements: Identify the gate’s intended usage class (I-IV) according to UL 325, as this will dictate specific operator and safety device requirements. For example, a Class II gate installed at a public access site requires more rigorous safety mechanisms than a Class I residential gate.
Implement Entrapment Protection Devices: Equip every gate operator with at least one primary and one secondary entrapment protection device. For example, combining a photoelectric sensor (non-contact) with a gate edge (contact sensor) provides robust safety. Ensure these devices are regularly tested, as UL 325 mandates continuous monitoring.
Construct Gates with Safety in Mind: When building or selecting gates, ensure they meet ASTM F2200 design standards for clearances, reach-through prevention, and obstruction-free movement. These requirements help prevent common injuries associated with automated gates.
Maintain Documentation: Keep a record of all compliance checks, installation details, and safety tests. This is helpful for clients and inspectors, and it’s also useful in case of any future updates or maintenance.
Educate Property Owners and End Users: Provide training or clear instructions to the client on how to safely operate and maintain the gate. This includes reviewing basic safety functions, proper testing of entrapment devices, and a clear understanding of safety signs.
Common Missteps and How to Avoid Them
Skipping Regular Maintenance: UL 325 requires regular checks to ensure all safety features are functional. Neglecting this can lead to device failures, increasing the risk of accidents. Schedule periodic maintenance and testing for optimal safety.
Inadequate Entrapment Protection: Relying solely on one type of entrapment protection, like a reversing sensor, isn’t enough. UL 325 requires a combination of devices, which ensures that the gate reverses in case one device fails.
Improperly Positioned Access Controls: Controls should be far enough from the gate to prevent accidental activation or user exposure to moving parts. Position controls at least six feet from the gate to avoid unintended operation.
Not Checking Local Codes: Some regions may have additional requirements beyond UL 325 and ASTM F2200. Always confirm local code requirements before installation to avoid potential compliance issues.
Conclusion
Adhering to UL 325 and ASTM F2200 standards is more than a box to check—it’s a commitment to safety, quality, and professional integrity. By understanding and applying these standards, gate automation installers, contractors, and designers can build systems that protect users, satisfy regulatory requirements, and stand the test of time. Compliance isn’t just about following the rules; it’s about delivering safe, reliable, and trustworthy solutions for every project.
By committing to these standards, you not only safeguard your clients and users but also enhance your reputation as a skilled and conscientious gate automation professional.